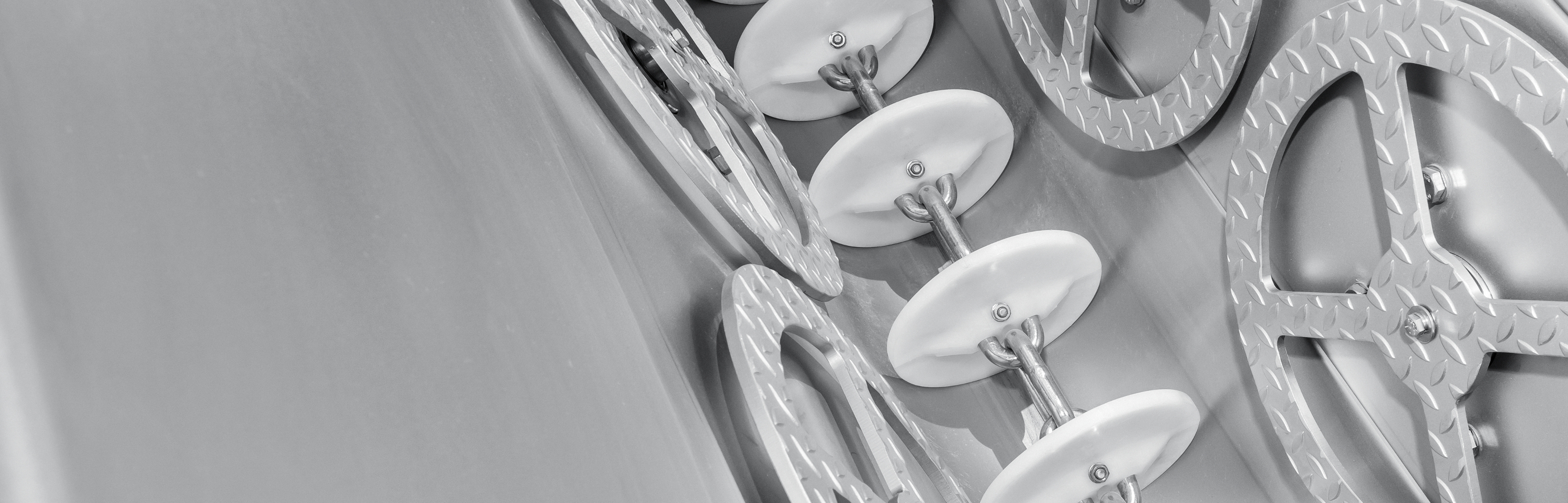
Infeed & discharge
Air discharge assistance
A breath of fresh air
There are materials out there that cling to our systems more than others. That’s where a controlled, nozzle-driven air jet can help make sure than even bulk materials with poor flowing properties will keep moving along or give sticky bulk materials a little push in order to remove them from the conveyor chain. And depending on the specific area, we can also deliver ATEX-compliant, gas-tight, and pressure-tight versions to meet your specific needs.
- Compact conveyor technology
- High level of self-cleaning
- supports Infeed & discharge
- Electric or pneumatic
- Dustproof, gas-tight, and pressure-tight
- Low maintenance
- Continuous material flow
- Breaks clumps
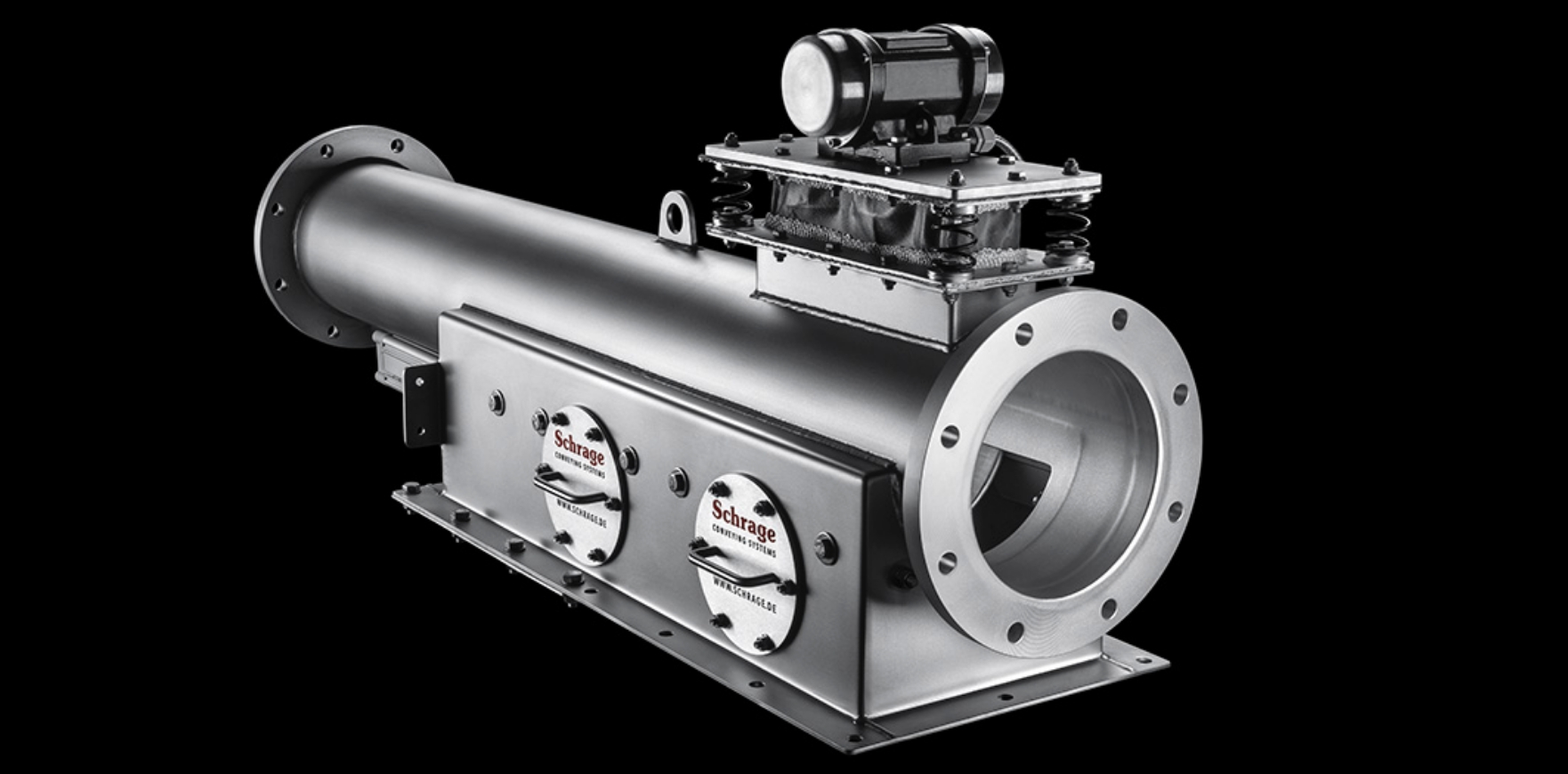
Beater discharge assistance
Tell them to knock it out.
Particularly sticky or caking materials need a bit of a push both when being fed and discharged. Our beaters, which are available in both pneumatic and electrical versions, are the perfect choice when it comes to loosening up compacted powder, get fine dusts moving, and apply vibration to remove sticky bulk materials from the conveyor chain.
Silo filling
A bridge too far.
Sludge and sticky bulk materials with poor pourability are often prone to bridging. In order to ensure continuous conveyance, we can optionally equip our tube chain conveyors with bridge breakers, better described as rotating stainless steel wheels with a textured surface that are moved by independent gearing and have adjustable speeds so that they can handle any bulk material.